Adotar estratégias para solucionar problemas e otimizar o desempenho da equipe é parte da rotina de todo gestor. Na indústria, isso significa implementar ações que melhorem os processos e que façam uma análise de falhas. Isso para que se reduzam as quebras e defeitos nos equipamentos.
Entretanto, essa tarefa pode ser um grande desafio. Por mais que seja feita uma manutenção preventiva, antecipar-se aos problemas é uma tarefa árdua.
Pensando nisso, mostraremos neste artigo o que é a análise de falhas, quais são os benefícios que ela traz, quais são as ferramentas utilizadas para a sua realização, os erros comuns que devem ser evitados, como implementá-la em sua empresa e quando e com que frequência ela deve ser feita. Confira!
O que é análise de falhas?
A análise de falhas é uma ação planejada que visa prevenir e avaliar não conformidades em processos. Portanto, a grosso modo, ela busca identificar a possibilidade de que algo aconteça fora do planejado, reconhecer o que seria esse desvio e levantar insights para tratá-lo. O objetivo é mitigar ao máximo esses problemas.
Podemos citar como exemplo o FMEA (do inglês “Failure Mode and Effects Analysis”), que estabelece alguns critérios para realizar essa análise. Muitas vezes, com base em falhas já ocorridas, sua aplicação visa impedir a recorrência de situações indesejadas. Para que isso seja feito com eficiência, alguns passos devem ser seguidos.
Quais são as etapas da análise de falhas?
Para começar, uma falha já identificada é descrita em detalhes. Verifica-se o que falhou, onde e quando isso ocorreu, qual foi a criticidade do problema, entre outros fatores. Na segunda etapa, são elaboradas as hipóteses para a causa do problema. Já na terceira, é hora de testá-las para que seja apontada a mais provável entre as levantadas.
Na sequência, a fase quatro é o momento de averiguar se há mecanismos para impedir a ocorrência da falha. Já na quinta etapa, são avaliados:
- Índices de recorrência
- Severidade
- Detecção
- Risco
A seguir, é hora de propor ações corretivas e preventivas. Para finalizar, é preciso implementar um processo de monitoramento. Essa última etapa é fundamental para garantir que as ações estabelecidas tenham sucesso.
Quais são os benefícios de se adotar esse método?
Para começar, o índice de recorrências tende a cair progressivamente. Na indústria, a quebra de equipamentos gera prejuízos enormes, que também podem ser evitados ou, pelo menos, reduzidos com essa ação estratégica. Dessa forma, a equipe de manutenção passa a ser capaz de trabalhar com mais planejamento.
Em vez de atuar sempre de forma corretiva, interrompendo a produção, os técnicos conseguem agendar ações preventivas e verificar questões levantadas nas análises. Consequentemente, o ritmo de produção se mantém mais fluido.
Por fim, o principal benefício é, sem dúvida, a redução de custos que essa medida traz. Quanto mais eficiente for a análise, melhor o desempenho da empresa como um todo. Então, o retorno sobre o investimento (ROI) em equipamentos tende a subir, o que dá mais competitividade à organização.
Por onde começar uma análise de falhas?
A análise de falhas, antes de qualquer coisa, é um processo evolutivo. É preciso alinhar os objetivos com os membros do time, desenvolver checklists e conscientizar sobre a importância de documentar cada análise.
Por sua vez, o monitoramento jamais pode ser ignorado — mesmo em ações corretivas da manutenção. O ideal é que haja um acompanhamento de perto para que a própria análise passe por uma melhoria contínua. Se uma medida não foi eficiente para reduzir uma falha, é hora de pensar em alternativas.
Quais ferramentas podem ser utilizadas para a análise de falhas?
Existe uma variedade de ferramentas de análise de falhas e solução de problemas. Para que os profissionais de manutenção e da área de confiabilidade possam selecionar a ferramenta correta e propor uma solução com maior eficiência e menor custo, os diferentes métodos devem ser descritos e comparados.
A verdade é que cada ferramenta tem seu funcionamento melhor em uma determinada condição. Portanto, o profissional responsável por essa análise deve saber como selecionar essas soluções e como combiná-las para chegar a uma conclusão tecnicamente satisfatória e, assim, tomar uma decisão.
Acompanhe a seguir as principais ferramentas para a análise de falhas:
Cinco Porquês na análise de falhas
Essa metodologia é usada para verificar a causa e os efeitos de uma falha específica. Ela consiste em perguntar o “porquê” de uma determinada situação, e a resposta forma a base para o próximo questionamento.
Por exemplo:
Pergunta 1: Por que a empresa está atrasando as entregas?
Resposta: Paralisação de um equipamento crítico.
Pergunta 2: Por que esse equipamento falhou?
Resposta: Falta de manutenção preventiva.
Pergunta 3: Por que a manutenção não foi aplicada corretamente?
Resposta: Falta de peças e outros equipamentos para reparo.
Pergunta 4: Por que a indústria deixou faltar essas peças e equipamentos?
Resposta: Ineficiência no controle de estoque.
Pergunta 5: Por que o controle de estoque não foi realizado da forma correta?
Resposta: A equipe não possui uma ferramenta que concentra todas as informações do inventário.
Diagrama de Ishikawa ou Espinha de Peixe
Também conhecido como “Espinha de Peixe”, o diagrama é uma ferramenta gráfica que serve para identificar possíveis causas, origens e quais variações específicas no processo representam a maior fonte de variabilidade na saída.
Um Diagrama de Ishikawa completo é composto por uma espinha central e ramos que parecem com o esqueleto de um peixe. Dessa forma, as ramificações categorizam as causas, sejam por função do processo ou sequência. Por sua vez, as causas potenciais são listadas e testadas para validação com o uso de evidências ou outra ferramenta analítica em cada categoria.
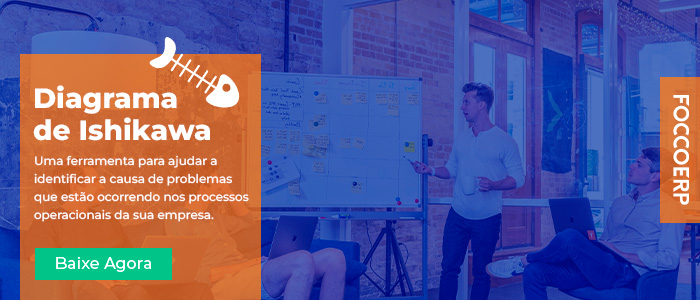
Árvore Lógica das Falhas
Trata-se de um processo para identificar as raízes físicas, humanas e latentes de um defeito. Primeiro declara-se o problema com a descrição do erro. Fazer isso com precisão das falhas funcionais é fundamental para o êxito da construção da árvore lógica.
Falhas funcionais são aquelas em que a máquina deixa de desempenhar a sua função no processo de produção. Por exemplo: uma bomba hidráulica deixa de bombear determinado fluído com a vazão requerida pelo projeto.
Com o mapeamento dessas falhas, desenha-se uma árvore lógica de acordo com os acontecimentos correlatos às mesmas.
Diagrama de Pareto
Também chamado de Análise de Pareto, essa é uma metodologia usada no intuito de quantificar e discutir as causas de um evento com o seu consequente efeito.
O objetivo é conflitar as causas de falhas com o número de paradas de uma máquina. Ou seja, com ela é possível enxergar quais são as causas que mais impactam na confiabilidade e disponibilidade do equipamento.
Por fim, o diagrama é uma representação gráfica dos desafios da gestão de processos em ordem de classificação do mais ao menos frequente, e demonstra a regularidade dos tipos de defeitos. Assim, você tem a oportunidade de decidir qual é o evento prioritário para ser solucionado.
Diagnóstico IA
Através de ferramentas IoT (Internet das Coisas) e IA, é possível identificar padrões e fazer uma análise minuciosa de aspectos básicos e complexos dos equipamentos a partir de dados. Esses dados podem ajudar a descobrir causas e efeitos das falhas, por exemplo, e contribuir para diagnósticos mais precisos sobre os erros.
Vale dizer ainda que esses dados podem ajudar na identificação de falhas em estágios iniciais, capacitando as equipes de manutenção a tomar medidas preventivas antes que ocorram falhas mais severas.
Qual a importância de fazer uma análise de falha?
A análise de falha é uma importante ferramenta para identificar erros que podem vir a prejudicar a continuidade, confiabilidade e qualidade dos processos industriais.
Ao descobrir as irregularidades, a empresa será capaz de agir com antecedência e elaborar ações preventivas que a ajudem a impedir a perpetuação dos erros e, consequentemente, a ocorrência das falhas.
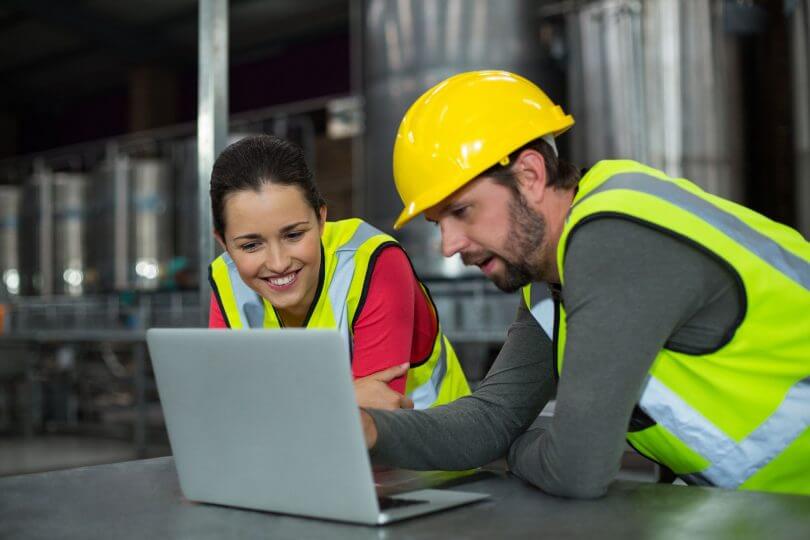
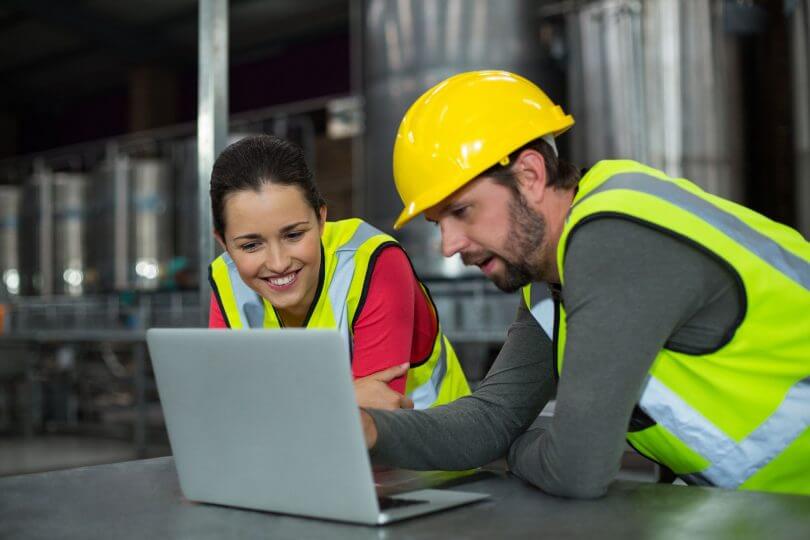
Por que uma análise de falhas precisa ser eficiente?
Uma análise ineficiente impede que a indústria identifique os gargalos que podem acarretar falhas e resultar na paralisação de suas máquinas, equipamentos e processos.
Essa paralisação, por sua vez, pode representar uma série de prejuízos, a começar pelo atraso das entregas, problemas de qualidade e perda de competitividade empresarial.
Essas paradas também podem gerar custos elevados associados a reparos, substituição de peças e manutenção corretiva, bem como perdas de produção e custos indiretos relacionados à inatividade.
Quais são as melhores práticas para realizar esse tipo de análise?
Com a finalidade de chegar a um diagnóstico de problema no funcionamento de máquinas ou instalações, como há uma grande variedade de conceitos e formas construtivas, não é possível padronizar procedimentos para essa análise.
Então, é preciso contar com mão de obra qualificada que tenha conhecimento necessário dos componentes do sistema e dos princípios de funcionamento para que, ao percorrer os circuitos, verifique a continuidade da energização ou o fluxo do fluido de trabalho, e possa chegar ao ponto onde tenha ocorrido o problema.
Assim sendo, ela tem a chance de confirmar suas suspeitas do que foi a causa e proceder com a reparação.
Quais os erros mais comuns que devem ser evitados?
Sabemos que muitas organizações acabam por não ter alternativa nem condições de sustentar uma manutenção bem estruturada, seja devido à limitação de recursos ou pelo fato de serem empresas de menor porte.
Por outro lado, existem organizações que até têm condições, mas, mesmo assim, preferem correr os riscos do “quebra, conserta”. Esses são os principais erros que devem ser evitados, visto que as perdas financeiras depois, fatalmente, serão maiores.
Como fazer uma análise de falhas?
Sabendo que a análise de falhas é uma ferramenta essencial para assegurar a qualidade dos processos, é momento da sua indústria estruturar um plano de ação para aplicá-la. Abaixo, preparamos um passo a passo simples que pode ajudar. Confira!
1. Identifique o problema
Quais problemas a sua empresa está enfrentando hoje: atraso na linha de produção? Atraso nas entregas? Baixa qualidade dos produtos? A primeira etapa consiste em identificar os gargalos atuais para que as estratégias sejam construídas em cima desses problemas.
Para identificar esses gargalos, sua indústria pode recorrer a dados e indicadores (KPIs), feedbacks de clientes e até mesmo os apontamentos de funcionários.
2. Verifique as possíveis causas
Depois que tiver feito o levantamento de todos os problemas, é hora de descobrir o que pode estar ocasionando esses gargalos. Nessa etapa, é importante que a avaliação seja o mais criteriosa possível para que a indústria não deixe passar nenhuma informação valiosa, e que realmente chegue à causa raiz dos problemas.
Assim como na etapa anterior, a empresa também pode usar dados e indicadores, mas uma avaliação presencial — acompanhando a performance e o desempenho das máquinas e equipamentos, por exemplo — pode ser ainda mais assertiva.
3. Analise se as hipóteses estão atreladas ao problema
Identificadas as possíveis causas, os profissionais responsáveis por fazer a análise precisam avaliar se as hipóteses fazem sentido e se elas realmente estão atreladas ao problema.
Qualquer causa não relacionada precisará ser descartada, primeiramente para não atrapalhar o desenvolvimento das ações preventivas e corretivas, e segundo para que a indústria não desperdice tempo, energia e recursos importantes.
4. Examine os controles existentes para impedir a continuidade da falha
Após separar as hipóteses que estão atreladas ao problema, será preciso que a equipe examine todos os elementos que controlam a execução dos processos. Essa atividade ajudará a avaliar se procedimentos, políticas e sistemas, por exemplo, estão em conformidade, e se existe algum tipo de lacuna nessas operações.
5. Avalie o erro
Assim que tiver examinado os controles existentes, será preciso avaliar o erro para entender o impacto e as implicações que ele acarreta à indústria.
Por exemplo, a falha em um equipamento crítico pode resultar em paradas não programadas ou acidentes de trabalho. A paralisação, por sua vez, pode impactar outros processos de produção, afetar a qualidade final do produto e gerar atrasos. Já a ocorrência de acidentes pode resultar em processos judiciais, perda de reputação no mercado, entre outros.
Para avaliar o erro a fundo, equipes podem recorrer a dados, indicadores e relatórios.
6. Desenvolva ações corretivas e preventivas
Feita a avaliação do erro, é momento então de estruturar ações corretivas e preventivas para solucionar os problemas e impedir que eles voltem a se repetir no futuro.
Ao desenvolver essas ações, os profissionais precisam definir em quais datas elas serão realizadas, quais procedimentos serão necessários, quais colaboradores estarão envolvidos, e qual o capital necessário para reparar os erros e aplicar as melhorias.
7. Acompanhe as ações corretivas e preventivas
Para assegurar que as ações corretivas e preventivas estão surtindo o efeito desejado, será necessário que as equipes façam o acompanhamento dessas ações. É a partir disso que vão conseguir, por exemplo, identificar todos os gargalos e reformular as estratégias para assegurar a melhoria contínua na indústria.
Esse acompanhamento pode ser feito a partir de indicadores de desempenho ou, até mesmo, visitas e inspeções no chão de fábrica.
Caso queira ampliar o alcance sobre as operações e garantir que todos estejam envolvidos na resolução de problemas, a liderança pode pedir o apoio dos colaboradores para reportar erros e inconsistências nas máquinas, sempre que forem identificados.
Quando esse tipo de análise deve ser feita e com que frequência?
Se for o caso de uma manutenção apenas corretiva, a gestão precisa definir alguns parâmetros para disparar a necessidade de fazer a análise de falhas conforme suas possibilidades, que poderiam ser:
- Máquinas classificadas com nível de criticidade “A”: todas as paradas por falhas devem ser analisadas;
- Máquinas classificadas com nível de criticidade “B”: analisar todas as paradas por falhas acima de duas horas;
- Máquinas com taxa de utilização de produção acima de 70%: fazer análise de falhas;
- Falhas que elevam o risco de segurança ou riscos ambientais: todas devem ser analisadas;
- Falhas com alto índice de repetitividade, por exemplo: acima de seis ocorrências no mês.
Portanto, é preciso estabelecer esses parâmetros, que devem ser definidos em conjunto entre os setores de manutenção, produção e gerência, para definir quando a análise de falhas será feita.
Como vimos, a análise de falhas é uma importante ferramenta que ajuda a indústria a assegurar a confiabilidade, a continuidade e a qualidade dos seus processos. A prática impede que erros se propaguem e prejudiquem o desempenho de máquinas e operações, e que esses gargalos venham a se tornar problemas críticos para o sucesso do parque fabril.
Se você quer implementar a análise de falhas dentro do seu próprio negócio, melhorar processos internos e tomar decisões mais inteligentes baseadas em dados, fale com um de nossos consultores e conheça o FoccoERP! A tecnologia foi desenvolvida por especialistas para ajudar a sua empresa a produzir de forma mais inteligente, e a maximizar o tempo e a rentabilidade.
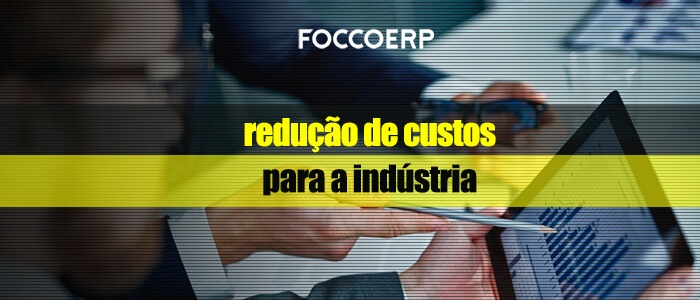
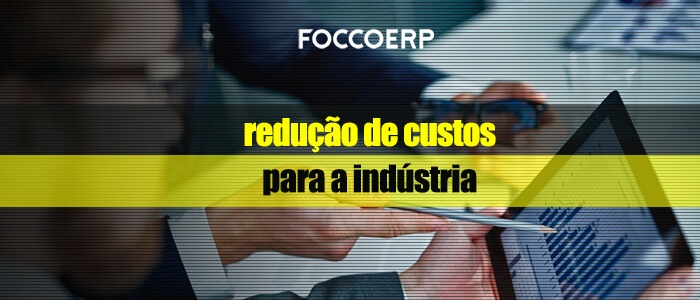