Gerenciar a cadeia de suprimentos pode ser uma tarefa complexa, até mesmo para os gestores mais experientes. Se por um lado a falta de materiais pode ocasionar paradas na operação e atrasos, o excesso de insumos pode resultar em desperdícios e perdas. Nesse cenário, o MRP pode ser um grande aliado na busca do equilíbrio na operação fabril.
O MRP é uma ferramenta utilizada em diversas indústrias, principalmente para o controle de estoques, aquisição de materiais e programação da produção. Apesar disso, muitas pessoas ainda não conhecem seu potencial e a melhor forma de aplicá-lo em seu próprio negócio.
Por isso, criamos este artigo, para explicar o que é, qual sua origem, como usá-lo, principais vantagens e muito mais. Aqui, você entenderá como esse conceito pode melhorar a eficiência operacional do seu negócio. Acompanhe!
O que é o sistema de MRP?
MRP é um conceito de gestão que planeja a necessidade de matéria-prima, capacidade de equipamentos e processos produtivos de uma fábrica. A sigla significa Manufacturing Resource Planning — Planejamento de Recursos de Produção, em português.
A ferramenta é usada no controle de estoque e na programação de produção, sendo responsável por mapear necessidades de suprimentos e projetar quantidades e tempos de fabricação. Ainda, com a tecnologia, é possível calcular as quantidades de componentes necessários para a fabricação de um produto, o que ajuda a evitar desperdícios e aumentar a margem de lucro.
O seu objetivo é manter a fábrica em constante operação, evitando que haja excesso ou falta de materiais.
O que é MRP I e II?
Há duas versões do sistema de Planejamento de Necessidades de Materiais.
O MRP I foca no cálculo da quantidade de itens que deve ser produzido, materiais necessários e prazos de entrega. Mesmo sendo mais simples, funciona para garantir uma produção enxuta, mas que atenda às necessidades da organização.
Já o MRP II abrange outras áreas, como os recursos da própria fábrica. Para tanto, ele considera fatores como capacidade de produção, mão de obra, maquinário e recursos financeiros.
Como surgiu o MRP?
Com o aumento significativo das atividades na indústria americana após a Segunda Guerra Mundial, as fábricas passaram a trabalhar com lotes de produção trimestrais. Eles eram baseados em previsões de demanda e tinham como objetivo produzir o equivalente a mais de 12 meses de pedidos.
No entanto, à medida que o volume de pedidos foi caindo, surgiram desafios na previsão e gestão de estoques, levando ao desenvolvimento de técnicas para gerenciar melhor o armazenamento. Assim, surgiu o conceito, ainda em seus primórdios, no início dos anos 1960.
Nos anos seguintes, com o avanço dos computadores, que permitiu o acesso a dados necessários, as técnicas e a documentação evoluíram. Nesse cenário, houve um grande movimento de discussão de um sistema MRP, visto em diversos artigos e debates em corporações dos Estados Unidos.
A partir daí, ganhou destaque com a introdução do MRP II, que incorporava os módulos MRP I e CRP (Capacity Requirement Planning). O CRP, dentro do conceito do MRP II, era responsável por calcular a capacidade produtiva de uma fábrica, verificando se existiam recursos suficientes para a execução.
Atualmente, MRP I e II fazem parte do conceito de ERP (Enterprise Resource Planning). O MRP é mais focado na gestão da produção, enquanto o ERP engloba todas as outras áreas da empresa, considerando a correlação entre elas.
Qual é a sua origem?
A origem está na aplicação da lógica da Bill of Materials (BOM), que, por meio do processo de explosão de materiais, decompõe o produto em seus níveis mais baixos, permitindo determinar o que comprar, em que quantidade e quando, para que a produção não sofra interrupções nem gere excesso de estoque.
Qual é o objetivo do MRP?
O objetivo do MRP é garantir que os insumos e componentes necessários para a produção estejam disponíveis no momento certo, na quantidade correta e com o menor custo possível.
Desse modo, ele busca:
- Evitar falta de materiais: para que a produção não seja interrompida por falta de insumos.
- Reduzir estoques excessivos: minimizando custos com armazenamento e desperdício.
- Sincronizar a produção com a demanda: ajustando os pedidos de compra e fabricação conforme a necessidade real.
- Melhorar a eficiência operacional: otimizando o fluxo de suprimentos e evitando gargalos na produção.
- Aumentar a previsibilidade: permitindo um planejamento mais preciso da cadeia produtiva.
Assim, ajuda as indústrias a equilibrar oferta e demanda, otimizando recursos e melhorando a competitividade no mercado.
Como é feito o cálculo do MRP?
O processo de cálculo dos recursos de produção passa por algumas etapas:
- Definição do produto final: o Plano Mestre de Produção (MPS) estabelece a produção planejada e sua quantidade.
- Identificação dos componentes: a BOM lista todos os insumos necessários.
- Cálculo da demanda de materiais: o MRP determina a quantidade exata de cada item.
- Verificação de estoques e tempos de reposição: o sistema analisa estoques disponíveis e necessidade de compras.
- Geração de ordens de compra e produção: emite pedidos para fornecedores e ordens internas de fabricação.
Quais as etapas do MRP?
O processo de cálculo do MRP segue 7 etapas consecutivas. Acompanhe!
1- Planejamento estratégico da produção
Nesta fase inicial, são definidas as metas de produção com base em previsões de demanda, custos, lucratividade e ciclo de vida dos produtos. Ainda, também analisam restrições de mercado, fornecedores e logística, garantindo um planejamento sólido.
2- MPS — Master Production Scheduling (Plano Mestre de Produção)
O Plano Mestre de Produção (MPS) estabelece o que será produzido, em que quantidade e quando, considerando projeções de vendas e a capacidade produtiva da empresa.
3- MRP — Material Requirements Planning (Planejamento das Necessidades de Materiais)
Aqui, ocorre a explosão de materiais, identificando os insumos e componentes necessários para cada produto. O MRP calcula o que comprar, em que quantidade e quando para evitar faltas ou excessos de estoque.
4- CRP — Capacity Requirements Planning (Planejamento da Capacidade Produtiva)
Além dos materiais, é preciso garantir que a empresa tenha recursos suficientes para atender à demanda planejada sem comprometer prazos e qualidade.
Desse modo, o CRP verifica a disponibilidade de mão de obra, máquinas, infraestrutura e padrões de qualidade, ajustando o plano, caso necessário, para garantir um fluxo produtivo eficiente e sem sobrecarga.
5- Geração e liberação de ordens de produção e compra
Após o planejamento, o sistema MRP emite ordens de produção e de compra para fornecedores e departamentos internos, organizando o fluxo de trabalho e garantindo que todos os insumos estejam disponíveis no momento correto.
6- Execução da produção e logística
As ordens são executadas e a produção começa. Nessa etapa, há um acompanhamento do andamento da manufatura, movimentação de insumos e distribuição de produtos finalizados, garantindo que o cronograma seja cumprido.
7- Monitoramento e ajustes contínuos
O planejamento não é estático. O sistema MRP monitora atrasos, mudanças na demanda, falhas na produção ou problemas de fornecimento, ajustando ordens e prazos conforme necessário. Essa etapa garante resiliência e eficiência operacional.
Onde se aplica o MRP?
É possível aplicá-lo em empresas de todos os tamanhos, em diferentes áreas e setores, como veremos a seguir.
Fábrica
Um dos seus principais usos ocorre nas indústrias, onde ele é aplicado para a fabricação de diversos itens. Aqui, a ferramenta auxilia em várias etapas da cadeia de valor, como:
- Planejamento da produção: definição do fluxo produtivo e cronograma de fabricação.
- Aquisição de matéria-prima: cálculo preciso dos insumos necessários.
- Otimização de recursos: melhor aproveitamento de materiais e redução de desperdícios.
- Gestão de estoques: controle dos níveis de insumos e produtos acabados.
Além disso, fornece dados detalhados que permitem calcular com precisão as quantidades necessárias para a produção. Ele também cobre todas as principais frentes da cadeia produtiva:
- o estoque fornece informações detalhadas sobre os materiais disponíveis;
- o planejamento da produção estabelece um plano detalhado para as atividades fabris;
- o controle da produção monitora o andamento do processo, permitindo identificar e corrigir problemas rapidamente.
Logística
A ferramenta desempenha um papel essencial na organização da logística, ajudando a reduzir gargalos e otimizar custos. Suas principais funções incluem:
- Previsão de demandas: permite antecipar a necessidade de insumos e produtos.
- Gestão de pedidos: facilita o controle e a organização das entregas.
- Agilidade nas entregas: melhora a eficiência dos processos logísticos.
- Visão global dos estoques: garante um melhor alinhamento entre produção e distribuição.
Administração
Embora seja mais comum na indústria e na logística, também pode ser aplicado na administração para gerenciamento de estoques e planejamento estratégico, garantindo que a empresa atenda às necessidades dos clientes de forma equilibrada e eficiente. Seus principais benefícios incluem:
- Controle contínuo dos estoques: monitora a disponibilidade de produtos e evita rupturas no abastecimento.
- Equilíbrio entre oferta e demanda: ajusta a reposição de produtos conforme as necessidades dos clientes, evitando excessos ou faltas.
- Maior eficiência na tomada de decisões: fornece dados em tempo real para apoiar o planejamento e garantir um estoque alinhado com a demanda real.
Assim, o MRP otimiza a cadeia produtiva e melhora a gestão administrativa, garantindo que a empresa opere de forma sustentável e atenda melhor seus clientes.
Qual é o momento certo para implementar um MRP?
Quando a empresa atingir processos produtivos de média e alta complexidade, ou seja, indústrias de médio a grande porte. Isso acontece, pois, como há ciclos produtivos com diferentes níveis de dificuldade e uso de recursos diversos, a tecnologia pode auxiliar em cada um deles.
Tal feito não seria possível ser executado por humanos, dada a grande escala de produção. Daí surge a necessidade em implementar uma solução de planejamento completa.
No mais, pode ser de grande ajuda para instituições que estejam enfrentando desafios relacionados à movimentação interna de materiais, gestão de compras e gerenciamento de custos em suas linhas de produção complexas.
Como implantar o MRP em empresas?
Implementar um Material Requirements Planning vai transformar a gestão de produção e estoques da sua empresa. Com um ERP que já inclui funcionalidades de MRP, o processo se torna mais simples e eficiente, garantindo maior controle e previsibilidade.
Passos para a sua implantação
Avaliar as necessidades do negócio:
- Identificar gargalos na produção e desafios no controle de estoques;
- Mapear a demanda e entender como pode otimizar o fluxo produtivo.
Escolher um ERP com MRP integrado:
- Médias e grandes empresas podem se beneficiar de um ERP que já conta com MRP, evitando sistemas separados e reduzindo custos;
- a integração facilita a gestão e melhora a eficiência operacional.
Configurar corretamente a Bill of Materials (BOM):
- Estruturar os produtos e seus componentes para que o sistema calcule com precisão os materiais necessários;
- Garantir que os tempos de produção e os níveis de estoque estejam corretamente parametrizados.
Definir o Plano Mestre de Produção (MPS):
- Estabelecer um cronograma de produção realista e alinhado à demanda;
- Ajustar automaticamente a compra de insumos conforme as necessidades da fábrica.
Automatizar estoques e compras:
- Com um ERP integrado, o MRP calcula automaticamente quando comprar materiais e emitir ordens de produção;
- Reduz desperdícios e evita a falta de insumos.
Treinar a equipe e monitorar os resultados:
- Capacitar os times para utilizar o sistema de forma eficiente;
- Ajustar os processos conforme a evolução da produção e da demanda.
Quais são as diferenças entre MRP e ERP?
Quem é familiarizado com a tecnologia, certamente, reconhece a sigla ERP (Enterprise Resource Planning), um tipo de software voltado para gestão de negócios e automação de tarefas.
É comum que essas duas siglas sejam confundidas. No entanto, apesar de serem conceitos semelhantes, existem algumas diferenças que merecem e precisam ser consideradas. Confira!
Foco
O MRP tem como principal utilidade medir e planejar as necessidades de materiais, ou seja, o seu foco está na produção e em áreas relacionadas, como logística e estocagem. O ERP, por sua vez, visa gerir o negócio como um todo, englobando diversos setores, como RH, vendas, compras, logística e financeiro.
Funções principais
A função principal do MRP está limitada a calcular as necessidades de materiais, usando parâmetros como demanda e disponibilidade de equipamentos. Já o ERP, além de possuir essa funcionalidade, inclui várias outras, como automação de tarefas e gestão financeira, sendo útil em processos de outras áreas.
Objetivo
Enquanto o objetivo do MRP é otimizar o fluxo de produção e evitar o acúmulo ou falta de estoque, o ERP visa aumentar a eficiência operacional do negócio como um todo. O Enterprise Resource Planning fornece uma visão ampla sobre todas as operações, permitindo que os gestores tomem decisões embasadas em dados.
Integração
O MRP pode ser um módulo dentro de um software de ERP, ou seja, uma das muitas funcionalidades oferecidas por esse tipo de sistema. Dessa forma, não é necessário contratar um serviço de MRP à parte, basta escolher um ERP mais completo.
Além disso, ele também pode ser integrado a outros sistemas da empresa, por exemplo, um CRM.
Quais são as vantagens do MRP?
As empresas que adotam o Planejamento de Recursos de Produção obtêm uma série de benefícios.
Controle de inventário
O MRP é uma das maneiras mais eficientes para gerir estoques, por isso, é amplamente utilizado nesse setor. Por meio dele, é possível monitorar e gerenciar as quantidades de cada item armazenado, garantindo que não faltem insumos na hora da fabricação dos produtos.
Planejamento de compras
O controle sobre o estoque permite que o gestor escolha o melhor momento para efetuar novas compras, com base na análise das necessidades de materiais. Desse modo, o planejamento é otimizado, sendo feito de forma mais rápida e simples. Além disso, os dados levantados permitem assegurar a quantidade correta a ser comprada.
Agilidade no processo
O MRP faz uma análise completa do processo produtivo, incluindo demanda de vendas, estoque e capacidade de produção. Como resultado, as empresas podem programar atividades com antecedência, como uma compra de insumos. Sem contar que ele facilita a identificação de erros que atrasam a operação.
Planejamento de produção
O planejamento é a etapa na qual são definidos diversos fatores relativos à produção em determinado período. O MRP pode otimizar esse processo, já que usa os dados coletados para indicar os insumos devidos em cada etapa do processo produtivo com alta precisão.
Programação de trabalho
Os dados fornecidos pelo MRP são úteis para tomadas de decisão, o que inclui o planejamento e a programação das atividades da empresa. Isso é possível, pois ele possibilita determinar uma sequência lógica de tarefas para cumprir com o que foi estipulado no planejamento de produção.
Gestão de recursos
A principal função do MRP é identificar e programar o uso de recursos conforme a necessidade em cada etapa da produção. Assim, a empresa faz uma gestão mais eficiente de seus recursos, sejam financeiros, insumos, equipamentos e até mesmo mão de obra, com o objetivo de obter a máxima produtividade de cada um deles.
Gerenciamento e documentação de dados
Dados sobre materiais, estoque, compras e produção são recolhidos pelo MRP, facilitando a organização dos documentos e sua consulta posterior. Além disso, quando associado a um software de ERP, o gestor tem o benefício adicional de optar pelo armazenamento em nuvem, evitando perdas e danos.
Compras mais econômicas
A gestão de compras de materiais amplia a visão sobre as necessidades futuras da empresa. Com isso, é possível programar as compras com antecedência, garantindo que haja tempo para uma pesquisa aprofundada sobre os fornecedores. Dessa forma, a empresa tem a chance de optar por aqueles com melhor preço.
Economia de tempo
A gestão de matéria-prima, equipamentos e afins, feita pelo MRP, levaria muito mais tempo sem as devidas ferramentas tecnológicas. Logo, seu uso é uma forma de ganhar agilidade no chão de fábrica e reduzir gargalos, garantindo o cumprimento dos prazos de entrega e a satisfação do cliente.
Quais são as desvantagens do MRP e como superá-las?
Embora o MRP seja essencial para otimizar a produção e o controle de estoques, algumas dificuldades podem surgir quando ele não está integrado a um ERP completo.
Veja os desafios e como resolvê-los com a ferramenta certa.
Dependência da qualidade dos dados:
- O MRP só funciona bem se as informações forem precisas;
- Com um ERP integrado, a coleta e atualização de dados são automáticas, reduzindo erros manuais.
Alto custo de implementação:
- Softwares isolados de MRP exigem altos investimentos em aquisição e manutenção;
- A solução ideal é um ERP que já tenha MRP, eliminando custos adicionais e simplificando a gestão.
Complexidade na configuração:
- Pequenas e médias empresas podem enfrentar dificuldades ao configurar um MRP do zero;
- Com um ERP intuitivo e suporte especializado, a implementação se torna mais simples e eficiente.
Sensibilidade a variações na demanda:
- Se a demanda muda constantemente, o MRP pode gerar falta ou excesso de materiais;
- O ERP com MRP integrado ajusta estoques e compras automaticamente, garantindo equilíbrio.
Necessidade de integração com outros sistemas:
- O MRP precisa estar conectado a compras, vendas e estoques para funcionar bem;
- Um ERP que unifica todos esses processos garante um fluxo contínuo de informações e decisões ágeis.
A solução? Um ERP com MRP integrado, que elimina complexidade, reduz custos e garante um planejamento eficiente, tornando sua empresa mais produtiva e competitiva.

Qual é a vantagem de integrar MRP e ERP?
Ao combinar as vantagens de um serviço de MRP integrado ao ERP, a empresa pode obter resultados surpreendentes.
Processamento ágil de dados
O MRP consegue processar uma grande quantidade de dados rapidamente. Dessa forma, é possível calcular todos os materiais necessários, em um prazo muito mais curto do que um humano seria capaz, e sem abrir mão da acuracidade. Isso resulta em um ganho significativo de eficiência, otimizando o processamento do planejamento.
Diminuição das falhas humanas
Tarefas feitas exclusivamente por pessoas, sem auxílio de um sistema, costumam apresentar alta taxa de erros, o que leva a diversas refações. Com o MRP integrado ao ERP, esses erros são minimizados, uma vez que um sistema inteligente, criado com esse propósito, é responsável pela maioria das atividades. De modo geral, essas falhas só ocorrem quando os usuários inserem dados incorretos.
Redução dos custos de estoque
O MRP considera a política de lotes econômicos, sendo assim, a empresa reduz os gastos relativos ao armazenamento de material. As políticas de estocagem mínima e máxima, junto às informações sobre estoque de segurança e lote mínimo, fazem com que haja precisão nos cálculos sobre o que precisa ser adquirido, poupando os recursos da companhia.
Quais são os tipos de estrutura de MRP?
Existem diversos tipos de estruturas e todas estão relacionadas a três fatores:
- Etapas de produção;
- Design dos produtos;
- Lista de materiais necessários.
Apesar de uma ampla variedade, existem três tipos que se destacam. Confira!
Forma “A”
Essa forma é comum em indústrias nas quais um grande número de insumos diferentes dão origem a poucos produtos acabados. Um exemplo é a indústria de cosméticos, onde diversos insumos, incluindo princípios ativos, extratos vegetais, fixadores, fragrâncias e outros materiais são necessários.
Formas “T” e “V”
Já com as formas “T” e “V” é o contrário: poucas matérias-primas dão origem a uma ampla diversidade de produtos finais. Nesse caso, o processo produtivo é uniformizado, garantindo baixa variação entre os itens fabricados. Como exemplo, podemos citar a indústria de alimentos, onde itens básicos, como milho, trigo ou leite, dão origem a uma infinidade de produtos derivados.
Forma “X”
A forma “X” utiliza uma ampla variedade de matérias-primas, porém, os produtos finais obtidos são pensados para suprir necessidades específicas dos seus clientes. Esse modelo pode ser aplicado na produção de itens customizados e feitos por encomenda, por exemplo.
Quanto custa implementar o MRP?
O principal custo associado à implementação é a aquisição do software. Como dito, optar por um sistema ERP com módulo de Planejamento de Necessidades de Materiais pode ser uma estratégia vantajosa, uma vez que é possível combinar os benefícios das duas ferramentas.
O preço pode variar bastante, visto que isso depende da empresa provedora da tecnologia e do quão robusto é o sistema. Os mais simples são mais baratos, enquanto os mais completos costumam ser mais caros.
Desse modo, é preciso considerar as necessidades do negócio para fazer uma escolha correta. Na maioria das vezes, grandes indústrias se beneficiam de sistemas mais abrangentes.
Além disso, é possível que haja custos adicionais de customização para adequar o software às especificidades da empresa e também custos com licenciamento, pois, em alguns casos, é cobrada uma taxa, que pode ser única ou recorrente.
Afinal, vale a pena investir em MRP?
Sim, vale a pena! Principalmente se a sua empresa enfrenta problemas na gestão de estoque ou você quer evitar que isso aconteça. A adoção dessa tecnologia é pode transformar a realidade da fábrica, otimizando os recursos e maximizando resultados. De qualquer forma, o payback do investimento costuma ser rápido, aumentando as vantagens de sua implementação.
Ademais, O MRP é uma ferramenta completa para controlar estoques, aquisição de materiais e programação da produção. A solução traz diversos benefícios para o negócio, como agilidade no processo, redução de custos e minimização do desperdício. Ainda, seu uso pode sanar uma das maiores dores para os gestores de fábricas: perda de estoque.
Portanto, empresas de todos os tamanhos podem se beneficiar com o uso dessa solução, principalmente se associada a um sistema de ERP. O MRP permite que a organização faça bom uso de seus recursos para garantir uma empresa produtiva e lucrativa.
Quer elevar a eficiência operacional da sua empresa a um novo patamar? Solicite agora mesmo uma demonstração do FoccoERP, uma solução abrangente, que atende todos os setores e possui uma ferramenta de planejamento das necessidades dos materiais (MRP).
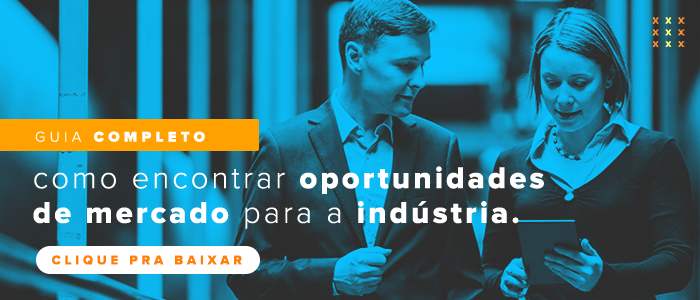